Project background
In 2020, responding to market requirements and the competition’s offer, Sinterit started working on the re-design of its flagship Lisa Pro printer. The new printer had to meet the growing demands of customers and meet the company’s business goals. Shortly before starting the project, I became a designer in the R&D department, so I had the opportunity to work both on the design of the printer and its software. Thanks to this, I understood the product well – its possibilities, but above all its limitations. A holistic view allowed us to better solve problems and face challenges arising during the project. It was an extremely satisfying job because I saw how the design process translates into a real product on an ongoing basis.
Project team:
Karol Wadycki – Product Designer
Agnieszka Surma – Junior UI/UX Designer
Photos:
Zbigniew Lewczak, Sinterit
Client:
Sinterit
Challanges
Lisa X is a printer for industrial needs but in compact shape. It was crucial to make professional 3D printer as easy to use as possible in industrial environment but still comfortable to use by experienced users. Thanks to intuitive design Lisa had to be great solution for both – education and professional industry.
Long story short
Project issues:
- To use professional 3d printer in SLS technology it is necessary to do many precise procedure.
- The printer has many consumables that should be replace on time. It must be easy to perform all basic maintenance by user.
- Training time is very expensive, so the entry level should be low. Workflow should be intuitive and easy for beginner but comfortable for experienced users.
Solutions:
- Step by step user guide through the pre-printing process. Automatic printer homing for printing.
- Components self-check to ensure that the printer components are ready to print and that printout will be printed correctly.
- Components spanlife counters – user will not be able to print if components are near to spanlife end.
- Intuitive user guide for all maintenance.
- Build-in guide how to clean the printer and how to remove material for material changing procedure.
- Expert Mode – allows operating faster on the printer – it is useful for advanced users which know the printer on a high level
- Lisa X uses pop ups and toast to communicate its status. All actions performed by users are confirmation.
My role
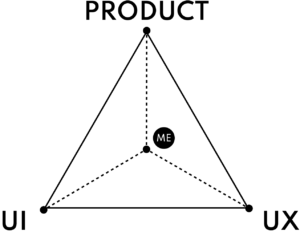
Define of user needs
Based on the information collected from the product, sales and customer support departments, I participated in defining the user’s needs.
Project & Design System.
In the project, I was the main designer, responsible for designing the functionality, style guide and the basic Design System, on which two applications for Sinterit printers were based. I also designed the information architecture based on user flow.
Overseeing the implementation of functionality.
I created executive documentation for developers. I took part in verifying the progress of implemented functionalities and setting priorities.
Project scope planning.
I made WBS to help project manager understand the project and prepare schedule.
Team management.
I managed the work of a member of my team, together with whom I designed the interface.
Test and bugs report.
In the initial phase of project implementation, I coordinated reporting and solving bugs in the application.
Usability tests.
After each significant stage of implementation, I conducted tests with respondents, verifying the implementation and addressing the needs that appeared during the tests.
Challanges
The printer interface is one of the most important elements, because good communication with the machine is the basis for safe and efficient work, which is required in a professional environment. As a designer, I faced the challenge of inventing and designing many functionalities so that the user could achieve their goals.
Key challanges:
- A many of precise actions required to operate the device
- High level of user error prevention required (security and reliability)
- Cooperation with other devices in the set
User Personas
In the project, I prepared personas based on information from Product and Marketing department.
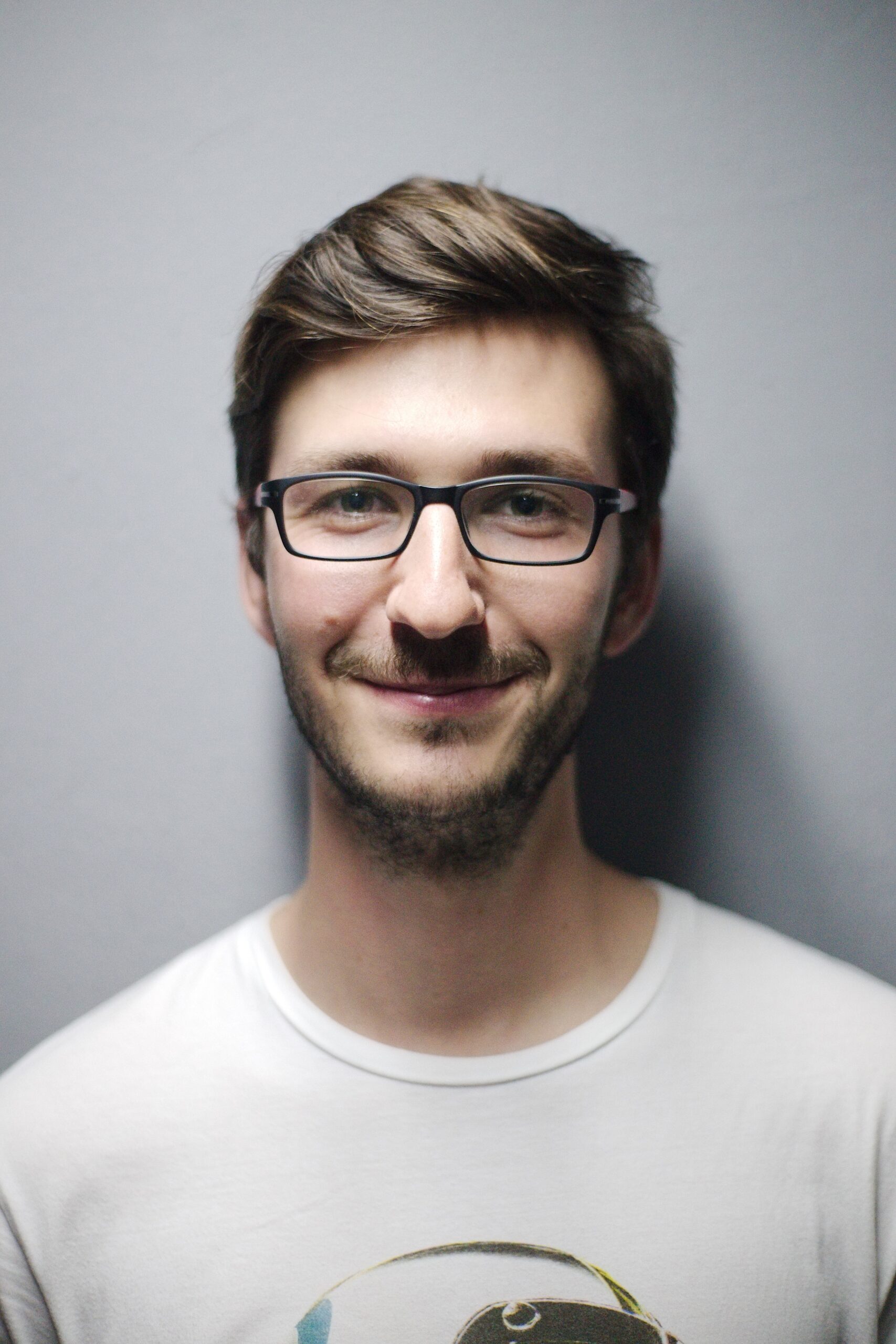
Dietmar, 30 – Industrial Product Designer
Goals
He is looking for a tool that will enable him to prototype faster.
Description
He has a unique blend of technical and artistic skills. He has wide range of knowledge but he is not engineer
Challanges
- He needs to rapid prototyping.
- He is not 3D printer specialist.
- He has limited time for projects, so a quick presentation of the concept is crucial for him.

John, 45 – Academic lecturer
Goals
He wants to teach his students 3D printing technology and is involved in innovative projects.
Description
He runs a 3d laboratory and is passionate about new technologies. He is really engaged in his work
Challanges
- Budget for his research
- Adjust the subject of your classes to business requirements
- Keep students interested
Research
I started my work with tests on the current printer. Usability tests allowed to identify all the strengths and weaknesses of the current interface. Based on the conclusions and recommendations, together with the team, we defined the basic assumptions on which we based the project.
Analysis:
- System status was not properly communicated. There are no headers informing where the user is.
- The structure of the current application was very tunnel-like – after starting an activity, it was impossible to finish it or move freely around the application – the only option was to undo.
- No error prevention – the application did not confirm the status of the operation, and did not communicate if a given action could lead to the failure of a given task.
- Each performed action must be confirmed.
- Errors communicated in real time via pop-ups
- The system must be interactive – the user must have control over the operations he performs and be able to move freely around the application.
Workshops
Knowledge about the customer and the user inside the organization is usually very large. The problem, however, is its large dispersion and different points of view that may obscure the whole picture. To make a synthesis, I organized workshops with members of various departments in the company to better look at the recipient of our product.
User flow developed during the workshop:
User stories created during the workshop were compared with existing solutions to show points in the process that need to be worked on.
Information architecture
Architecture of information based on simply functional divided.
- Printing
- Service and maintenance
- Settings
Design solutions
- The printer interface has been divided into 3 main parts, according to the functional division: Printing, Maintenance, Settings.
- The app guides the user step by step through the all process.
- Two work modes – Basic Mode for beginner user and Expert Mode for experienced users.
- The application ensures that the printer is maintained in good working order – signaling the spanlife of components and instructions for their replacement.
- Pop-ups and toasts keep the user informed about the status of the machine.
User guide for printing preparation
The comprehensive and precise preparation process has been designed in the form of step-by-step instructions. This keeps the entry level low and user training time reduced. Complicated and time-consuming training is not required.
Components lifespan monitoring
To make every print perfect it is neccesery to keep the printer in good condition. Every consumable component has lifespan counter so production and maintenance could be planned in advanced.
Listed components have parts description and build-in, step-by-step user guide thanks to every users can perform it.
Expert Mode
For more experienced users who want to work faster and do not need additional manuals, an expert mode has been prepared. In this mode, all additional security features and instructions have been disabled. For security, Expert Mode is marked with yellow frames and warnings.
Thanks to Expert Mode preparing time has been reduced for 80%.
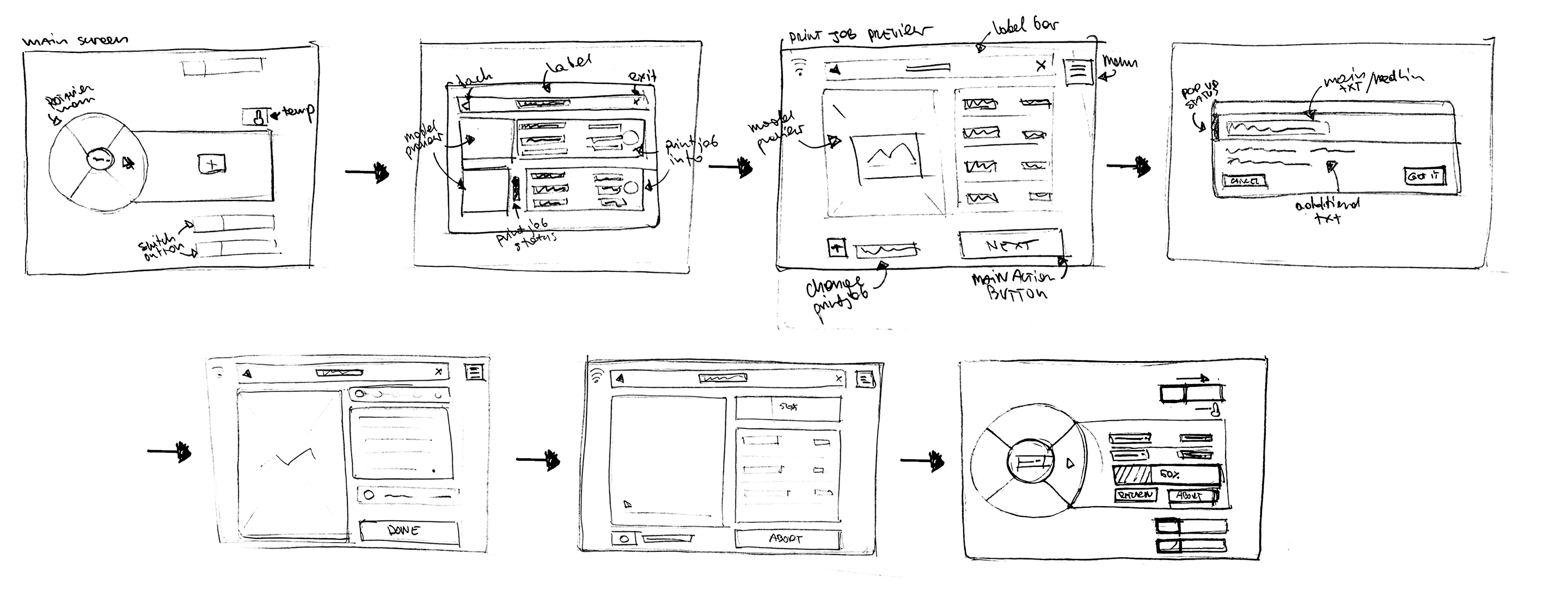
Interface - process layout
New print process – key user flow
- Side bar indicates printer status. Contains the necessary information.
- Navigation bar. Shows screen label, back arrow and exit button.
- Menu. Allows to navigate through the application
- Process progress bar. Indicates a process step
- Text block.
- Tools and tips. Indicates proper tools to perform operation
- Main button. Action button, places always on bottom right corner
- Animation. Helps users to perform operation i proper way. Indicates component place.
Summary
I spearheaded a comprehensive project aimed at optimizing the usability and functionality of the Lisa Pro printer at Sinterit, in response to market demands and competition. By leveraging internal workshops and research, I tailored solutions to various user groups, from students to small business owners and factory operators. My responsibilities encompassed defining user needs, overseeing the design process, and implementing intuitive interfaces. Through data-driven approaches and usability testing, we significantly improved user interaction with the printer, resulting in enhanced usability and satisfaction throughout the project. The Lisa X project introduced innovative features like expert mode, component lifespan monitoring, and step-by-step guides, revolutionizing user experience and boosting productivity in professional settings.
Thank you!🎉
Thank you for your time, if you have any further questions regarding my work, please feel free to contact me!